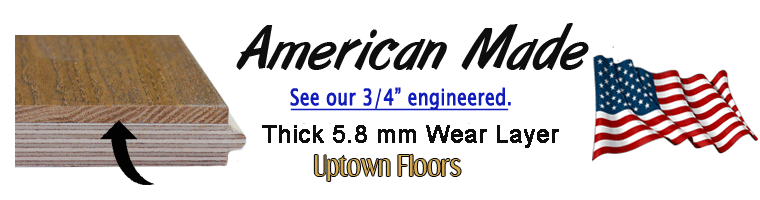
All times are UTC - 5 hours |
![]() ![]() |
Page 1 of 2 |
[ 23 posts ] | Go to page 1, 2 Next |
|
Author | Message | ||||
---|---|---|---|---|---|
supertruper |
|
||||
Joined: Wed Aug 09, 2006 8:33 pm Posts: 7 |
|
||||
Top | |
||||
![]() |
Gary |
|
||||
Joined: Sat Sep 25, 2004 7:42 pm Posts: 4373 Location: Antioch, CA. 94509 |
|
||||
Top | |
||||
![]() |
supertruper |
|
||||
Joined: Wed Aug 09, 2006 8:33 pm Posts: 7 |
|
||||
Top | |
||||
![]() |
Floorguy |
|
||||
Joined: Thu Aug 05, 2004 5:44 am Posts: 3509 Location: Austin |
|
||||
Top | |
||||
![]() |
supertruper |
|
||||
Joined: Wed Aug 09, 2006 8:33 pm Posts: 7 |
|
||||
Top | |
||||
![]() |
ChuckCoffer |
|
||||
Joined: Fri Aug 06, 2004 6:19 am Posts: 703 |
|
||||
Top | |
||||
![]() |
supertruper |
|
||||
Joined: Wed Aug 09, 2006 8:33 pm Posts: 7 |
|
||||
Top | |
||||
![]() |
Gary |
|
||||
Joined: Sat Sep 25, 2004 7:42 pm Posts: 4373 Location: Antioch, CA. 94509 |
|
||||
Top | |
||||
![]() |
ChuckCoffer |
|
||||
Joined: Fri Aug 06, 2004 6:19 am Posts: 703 |
|
||||
Top | |
||||
![]() |
Gary |
|
||||
Joined: Sat Sep 25, 2004 7:42 pm Posts: 4373 Location: Antioch, CA. 94509 |
|
||||
Top | |
||||
![]() |
ChuckCoffer |
|
||||
Joined: Fri Aug 06, 2004 6:19 am Posts: 703 |
|
||||
Top | |
||||
![]() |
Gary |
|
||||
Joined: Sat Sep 25, 2004 7:42 pm Posts: 4373 Location: Antioch, CA. 94509 |
|
||||
Top | |
||||
![]() |
supertruper |
|
||||
Joined: Wed Aug 09, 2006 8:33 pm Posts: 7 |
|
||||
Top | |
||||
![]() |
Gary |
|
||||
Joined: Sat Sep 25, 2004 7:42 pm Posts: 4373 Location: Antioch, CA. 94509 |
|
||||
Top | |
||||
![]() |
supertruper |
|
||||
Joined: Wed Aug 09, 2006 8:33 pm Posts: 7 |
|
||||
Top | |
||||
![]() |
![]() ![]() |
Page 1 of 2 |
[ 23 posts ] | Go to page 1, 2 Next |
All times are UTC - 5 hours |
Who is online |
Users browsing this forum: No registered users and 3 guests |
You cannot post new topics in this forum You cannot reply to topics in this forum You cannot edit your posts in this forum You cannot delete your posts in this forum |