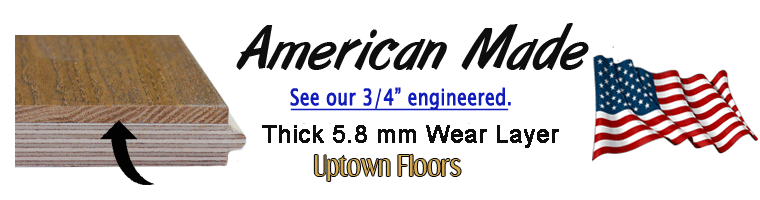
All times are UTC - 5 hours |
![]() ![]() |
Page 1 of 2 |
[ 29 posts ] | Go to page 1, 2 Next |
|
Author | Message | ||||
---|---|---|---|---|---|
SK Olson |
|
||||
Joined: Fri Sep 17, 2004 11:52 am Posts: 242 Location: Murphys, Calif. |
|
||||
Top | |
||||
![]() |
Floorguy |
|
||||
Joined: Thu Aug 05, 2004 5:44 am Posts: 3509 Location: Austin |
|
||||
Top | |
||||
![]() |
SK Olson |
|
||||
Joined: Fri Sep 17, 2004 11:52 am Posts: 242 Location: Murphys, Calif. |
|
||||
Top | |
||||
![]() |
Marco |
|
||||
Joined: Thu Mar 10, 2005 12:19 pm Posts: 138 Location: Los Gatos, Ca |
|
||||
Top | |
||||
![]() |
Gary |
|
||||
Joined: Sat Sep 25, 2004 7:42 pm Posts: 4373 Location: Antioch, CA. 94509 |
|
||||
Top | |
||||
![]() |
Ken Fisher |
|
|||||
Joined: Wed Aug 04, 2004 10:08 pm Posts: 1732 Location: Bonita Springs, Florida |
|
|||||
Top | |
|||||
![]() |
Charles A. Benghauser |
|
||||
Joined: Sun Jul 03, 2005 5:33 am Posts: 106 Location: Prescott, Arizona |
|
||||
Top | |
||||
![]() |
SK Olson |
|
||||
Joined: Fri Sep 17, 2004 11:52 am Posts: 242 Location: Murphys, Calif. |
|
||||
Top | |
||||
![]() |
Marco |
|
||||
Joined: Thu Mar 10, 2005 12:19 pm Posts: 138 Location: Los Gatos, Ca |
|
||||
Top | |
||||
![]() |
Ray Darrah |
|
||||
Joined: Thu Aug 19, 2004 6:02 pm Posts: 622 Location: Florida |
|
||||
Top | |
||||
![]() |
SK Olson |
|
||||
Joined: Fri Sep 17, 2004 11:52 am Posts: 242 Location: Murphys, Calif. |
|
||||
Top | |
||||
![]() |
Marco |
|
||||
Joined: Thu Mar 10, 2005 12:19 pm Posts: 138 Location: Los Gatos, Ca |
|
||||
Top | |
||||
![]() |
Gary |
|
||||
Joined: Sat Sep 25, 2004 7:42 pm Posts: 4373 Location: Antioch, CA. 94509 |
|
||||
Top | |
||||
![]() |
Ken Fisher |
|
|||||
Joined: Wed Aug 04, 2004 10:08 pm Posts: 1732 Location: Bonita Springs, Florida |
|
|||||
Top | |
|||||
![]() |
Ray Darrah |
|
||||
Joined: Thu Aug 19, 2004 6:02 pm Posts: 622 Location: Florida |
|
||||
Top | |
||||
![]() |
![]() ![]() |
Page 1 of 2 |
[ 29 posts ] | Go to page 1, 2 Next |
All times are UTC - 5 hours |
Who is online |
Users browsing this forum: No registered users and 0 guests |
You cannot post new topics in this forum You cannot reply to topics in this forum You cannot edit your posts in this forum You cannot delete your posts in this forum |