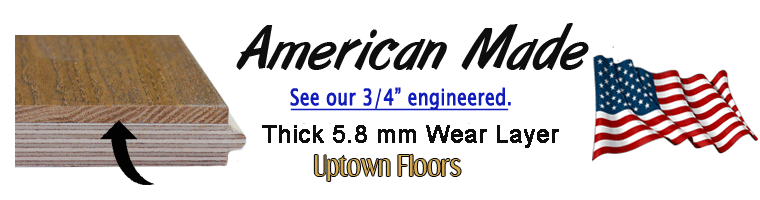
All times are UTC - 5 hours |
![]() ![]() |
Page 1 of 3 |
[ 32 posts ] | Go to page 1, 2, 3 Next |
|
Author | Message | ||||
---|---|---|---|---|---|
macknyt |
|
||||
Joined: Thu May 01, 2008 7:26 am Posts: 9 Location: Roanoke Virginia |
|
||||
Top | |
||||
![]() |
stonewood |
|
||||
Joined: Fri Jun 01, 2007 12:16 am Posts: 88 Location: Milwaukee,WI |
|
||||
Top | |
||||
![]() |
macknyt |
|
||||
Joined: Thu May 01, 2008 7:26 am Posts: 9 Location: Roanoke Virginia |
|
||||
Top | |
||||
![]() |
Floorguy |
|
||||
Joined: Thu Aug 05, 2004 5:44 am Posts: 3509 Location: Austin |
|
||||
Top | |
||||
![]() |
macknyt |
|
||||
Joined: Thu May 01, 2008 7:26 am Posts: 9 Location: Roanoke Virginia |
|
||||
Top | |
||||
![]() |
Floorguy |
|
||||
Joined: Thu Aug 05, 2004 5:44 am Posts: 3509 Location: Austin |
|
||||
Top | |
||||
![]() |
macknyt |
|
||||
Joined: Thu May 01, 2008 7:26 am Posts: 9 Location: Roanoke Virginia |
|
||||
Top | |
||||
![]() |
Barquios |
|
||||
Joined: Wed Nov 07, 2007 1:32 am Posts: 299 Location: Yakima, WA |
|
||||
Top | |
||||
![]() |
stonewood |
|
||||
Joined: Fri Jun 01, 2007 12:16 am Posts: 88 Location: Milwaukee,WI |
|
||||
Top | |
||||
![]() |
macknyt |
|
||||
Joined: Thu May 01, 2008 7:26 am Posts: 9 Location: Roanoke Virginia |
|
||||
Top | |
||||
![]() |
Gary |
|
||||
Joined: Sat Sep 25, 2004 7:42 pm Posts: 4373 Location: Antioch, CA. 94509 |
|
||||
Top | |
||||
![]() |
jperryrocks |
|
||||
Joined: Tue Jul 11, 2006 7:10 pm Posts: 83 |
|
||||
Top | |
||||
![]() |
macknyt |
|
||||
Joined: Thu May 01, 2008 7:26 am Posts: 9 Location: Roanoke Virginia |
|
||||
Top | |
||||
![]() |
Gary |
|
||||
Joined: Sat Sep 25, 2004 7:42 pm Posts: 4373 Location: Antioch, CA. 94509 |
|
||||
Top | |
||||
![]() |
macknyt |
|
||||
Joined: Thu May 01, 2008 7:26 am Posts: 9 Location: Roanoke Virginia |
|
||||
Top | |
||||
![]() |
![]() ![]() |
Page 1 of 3 |
[ 32 posts ] | Go to page 1, 2, 3 Next |
All times are UTC - 5 hours |
Who is online |
Users browsing this forum: No registered users and 0 guests |
You cannot post new topics in this forum You cannot reply to topics in this forum You cannot edit your posts in this forum You cannot delete your posts in this forum |