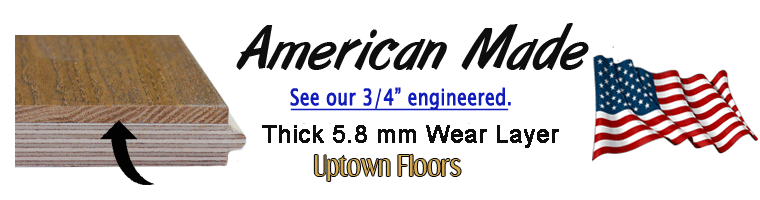
All times are UTC - 5 hours |
![]() ![]() |
Page 1 of 1 |
[ 13 posts ] |
|
Author | Message | ||||
---|---|---|---|---|---|
klondikepaul |
|
||||
Joined: Mon Jan 12, 2009 11:36 pm Posts: 6 |
|
||||
Top | |
||||
![]() |
dennis |
|
||||
Joined: Mon Apr 21, 2008 11:04 am Posts: 1272 Location: Richmond Hill, Ontario |
|
||||
Top | |
||||
![]() |
klondikepaul |
|
||||
Joined: Mon Jan 12, 2009 11:36 pm Posts: 6 |
|
||||
Top | |
||||
![]() |
klondikepaul |
|
||||
Joined: Mon Jan 12, 2009 11:36 pm Posts: 6 |
|
||||
Top | |
||||
![]() |
dennis |
|
||||
Joined: Mon Apr 21, 2008 11:04 am Posts: 1272 Location: Richmond Hill, Ontario |
|
||||
Top | |
||||
![]() |
Gary |
|
||||
Joined: Sat Sep 25, 2004 7:42 pm Posts: 4373 Location: Antioch, CA. 94509 |
|
||||
Top | |
||||
![]() |
klondikepaul |
|
||||
Joined: Mon Jan 12, 2009 11:36 pm Posts: 6 |
|
||||
Top | |
||||
![]() |
Gary |
|
||||
Joined: Sat Sep 25, 2004 7:42 pm Posts: 4373 Location: Antioch, CA. 94509 |
|
||||
Top | |
||||
![]() |
klondikepaul |
|
||||
Joined: Mon Jan 12, 2009 11:36 pm Posts: 6 |
|
||||
Top | |
||||
![]() |
Gary |
|
||||
Joined: Sat Sep 25, 2004 7:42 pm Posts: 4373 Location: Antioch, CA. 94509 |
|
||||
Top | |
||||
![]() |
dennis |
|
||||
Joined: Mon Apr 21, 2008 11:04 am Posts: 1272 Location: Richmond Hill, Ontario |
|
||||
Top | |
||||
![]() |
klondikepaul |
|
||||
Joined: Mon Jan 12, 2009 11:36 pm Posts: 6 |
|
||||
Top | |
||||
![]() |
Gary |
|
||||
Joined: Sat Sep 25, 2004 7:42 pm Posts: 4373 Location: Antioch, CA. 94509 |
|
||||
Top | |
||||
![]() |
![]() ![]() |
Page 1 of 1 |
[ 13 posts ] |
All times are UTC - 5 hours |
Who is online |
Users browsing this forum: No registered users and 0 guests |
You cannot post new topics in this forum You cannot reply to topics in this forum You cannot edit your posts in this forum You cannot delete your posts in this forum |